10 Benefits of Visual Progress Monitoring for Construction Stakeholders
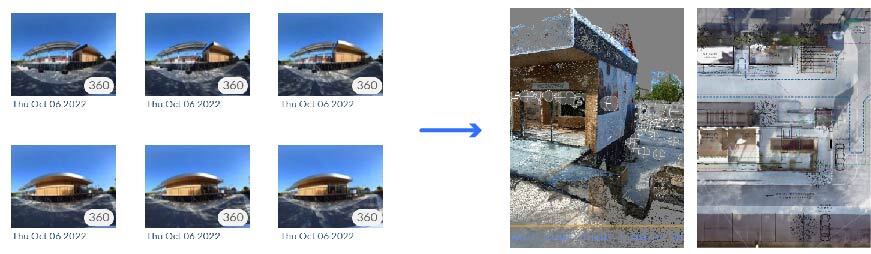
In construction, visual progress monitoring offers improved project visibility, management, and execution while reducing or eliminating the need for costly travel to the job site. This article will focus on the top ten benefits of visual progress monitoring, especially those enabled by reality mapping technology that brings the job site directly to remote stakeholders.
Key takeaways
- Visual progress monitoring refers to the ongoing visual assessment of a construction project.
- Top benefits of visual progress monitoring include real-time insights, better coordination and communication between off-site and on-site teams, improved productivity, better project outcomes, and cost savings.
- Optimal visual progress monitoring requires frequent, precisely-measurable reality capture of a job site so that completed work can be easily reviewed and verified against the plan. This process is simplified by selecting a photogrammetry engine that rapidly reads footage captured on everyday devices by regular on-site employees and transforms that data into measurable, as-built reality maps for indoor and outdoor work areas.
What is visual progress monitoring in construction?
In construction, visual progress monitoring enables remote, off-site stakeholders to visually track and assess the progress of construction projects. Visual progress monitoring begins with geo-referenced reality capture. During this process, an on-site person gathers video or image footage of the construction project. Often, such captures occur weekly.
It's important to note that virtually anyone can capture reality using simple, inexpensive equipment such as a smartphone, drone, or 360 camera. While there’s time and a place for expertly trained professionals to deploy laser scanners, visual progress monitoring does not necessarily need those devices. (Related: Selecting the right reality capture tool for the job.)
Once reality data has been captured and fed to the photogrammetry engine, a precise and measurable 2D floor plan and 3D digital twin of the construction project becomes available. These digital assets provide an immersive, accurate duplication of the job site perfect for visual progress monitoring. Of course, where and when available, reality models produced by laser scanning devices as well as structured light devices such as Matterport can be easily integrated into photogrammetry-produced data, creating a true time machine for construction.
Here are ten benefits unlocked by digital twin-enabled visual progress monitoring:
1. Real-time insights
Visual progress monitoring gives even the most remote project stakeholders total visibility into a project's current status. In an instant, project managers, owners, and owners' representatives can clearly understand the project's progress, rapidly identify potential issues, and make more informed decisions.
Related: Remote Construction Monitoring: The Key to Building Sweden's Tallest Office Tower
2. Enhanced coordination and communication
Because reality mapping engines produce a single source of truth for all stakeholders, visual progress monitoring facilitates better communication between teams. This is especially true of teams located in different places or answering to different executives.
Photogrammetry solutions integrated with design and schedule data, such as Reconstruct, allow stakeholders to pin concerns on visualized problems or rapidly share marked-up photos of urgent issues via text message.
Moreover, digital twins for construction make it easy to visually convey areas at risk for delays, the sequencing of upcoming works, and the most updated state of the project to team members, clients, investors, inspectors, and more so that:
- Plans can be collaboratively revised.
- The safety and constructability of the upcoming work can be carefully examined in a virtual environment.
- Teams can commit to a plan that can be easily coordinated with and communicated to all stakeholders.
Related: Learn more about Reconstruct’s collaborative tools.
3. Identifying root causes of schedule delay
Digital twins also help stakeholders pinpoint schedule delays and potential bottlenecks in the construction process. When such hold-ups are identified promptly or preemptively, project managers can take swift, corrective action by revising project schedules (e.g., changing work areas, re-sequencing work) to keep the project on schedule and avoid costly delays.
During meetings, project managers can use the digital twin to identify these concerns to other stakeholders.
4. Improved resource allocation and productivity
Visual progress monitoring enhances understanding of which tasks are lagging and which resources are underutilized. As a result, stakeholders can quickly come together to adjust resource allocation, identify under-utilized work areas, revise plans collaboratively, and then closely monitor progress for the next few weeks to ensure restored efficiency.
Visual progress monitoring connects the construction schedule and the work performed. This helps keep field teams on task and prepared for the regularly-scheduled reality capture from which their work will be measured and assessed.
Related: The Future of AI Project Monitoring in Construction
5. Optimized risk management
Because photogrammetry provides a visual representation of the project's current state, even remote stakeholders can quickly identify risks to budget, time, design, safety, and more. Analyzing progress trends and productivity over time using AI also allows potential schedule delay risks to be identified and communicated with the team so that corrective actions are taken. Such findings can be specified directly on the digital twin or summarized in a report.
The more frequently reality capture is performed, the more thorough and accurate the concerns identified and reported. When this occurs, top stakeholders can better assess current risks, anticipate potential challenges, and develop contingency plans to mitigate more significant risks down the road.
6. Better quality assurance and quality control
Visual progress monitoring frequently leads to better quality assurance and quality control. There are a variety of reasons for this. One is that on-site walk-throughs are often rushed or replete with distractions. Another is that many project teams are understaffed, and inspections of day-to-day operations are hard to keep up with. Lastly, without carefully reviewing “what is there on-site” vs. “what should be there, shown by design,” many issues--such as displacements of boxouts, conduits, and embedments, among others--go unnoticed, requiring teams to drill through finished surfaces, paying up to 30% extra for the rework. When remote stakeholders frequently and precisely walk through a job site without interruption or time crunch, they can:
- Carefully measure anything and everything.
- Pin RFIs and actionable insights directly on concerns.
- Overlay 2D and 3D designs against reality to detect errors and deviations.
- Turn back time to verify installations now concealed by concrete, floors, or ceilings.
What's more, any such findings can be quickly resolved. If concerns are severe, stakeholders can instantly escalate QA/QC concerns alongside visual proof.
7. Access to the entire construction timeline
When reality data is regularly captured, photogrammetry engines automatically organize footage in space and over time. The result? A precisely timestamped archive of a construction project from notice-to-proceed to commissioning and substantial completion.
Reconstruct Project Snapshot, for example, allows stakeholders to rewind progress to understand precisely how a project was built. If and when quality or safety concerns arise during visual progress monitoring, project managers can utilize this function to investigate problems further and determine the next steps rapidly. Post-construction, this feature also serves as the basis for identifying what’s behind the walls or buried under the ground.
This feature can save significant time, money, and resources by avoiding unnecessary investigative demolition and the repairs and rework associated with it.
8. Improved documentation and reporting
Project managers utilize progress monitoring software to better visualize the status of work on a construction site. When such monitoring occurs within cutting-edge reality mapping software, every pinned issue and corresponding resolution remain archived within the digital twin.
This reduces the need for repetitive administrative work and allows project stakeholders to focus on the most critical aspects of their jobs. Additionally, the timestamped visuals, organized across work areas, can be leveraged later to inform repairs and renovations, respond to tenant concerns and space management needs, regular condition assessments, and more.
9. Faster payment applications
Visual progress monitoring enables faster review of projects, creating a more rapid and transparent payment application process. Typically, this process starts with a subcontractor submitting a payment application validated by the general contractor. The application then moves through the General Contractor to an Owner/Architect/Contractor (OAC) meeting and then is reviewed by the architect and the owner or the owner's agent. Finally, the payment application is approved and processed.
This multi-step payment application process can be streamlined by offering a single source of readily available truth for all parties to review. Most importantly, project teams and contractors can be paid faster, alleviating some financial burdens caused by waiting 30 days or more on average for their payments to come through.
10. True transparency for remote stakeholders
While the day-to-day work of visual progress monitoring is typically assigned to certain project managers, they are not the only stakeholders interested in on-demand, immersive job site inspections. Everyone from architects and designers to building owners and investors can utilize digital twins for instant status updates… from anywhere in the world.
About Reconstruct
Reconstruct is the leading provider of visual progress monitoring for the construction industry. Unlike other providers, Reconstruct accepts reality data captured on virtually all devices, including smartphones and 360 cameras. This enables construction stakeholders with even the most modest budgets to reap the benefits of visual progress monitoring while reducing the need for costly, time-consuming travel.
Contact our team to learn more about Reconstruct or request a personalized demonstration.
Related Posts
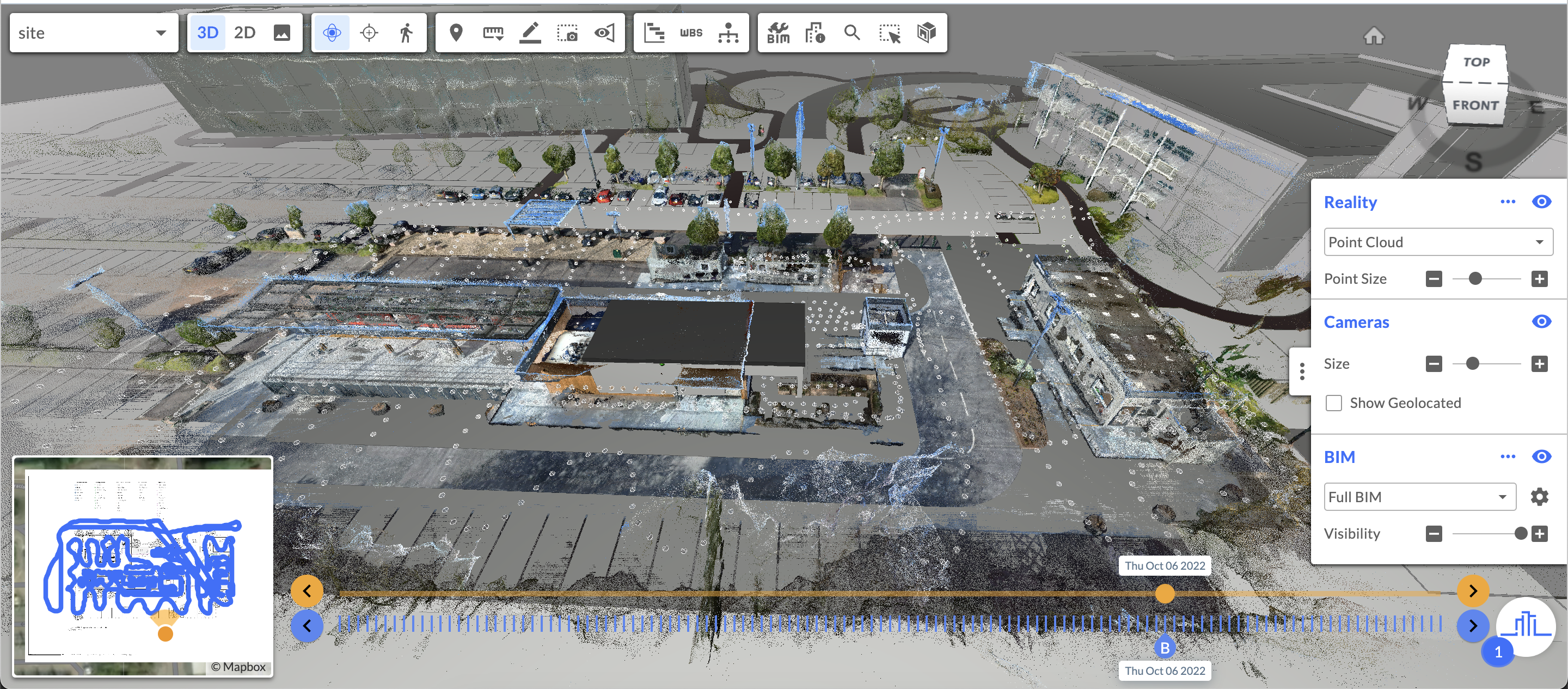
Benefits of 3D Scanning in Construction
The benefits of 3D scanning in construction include improved remote quality control, virtual progress monitoring, and protection against liability claims.
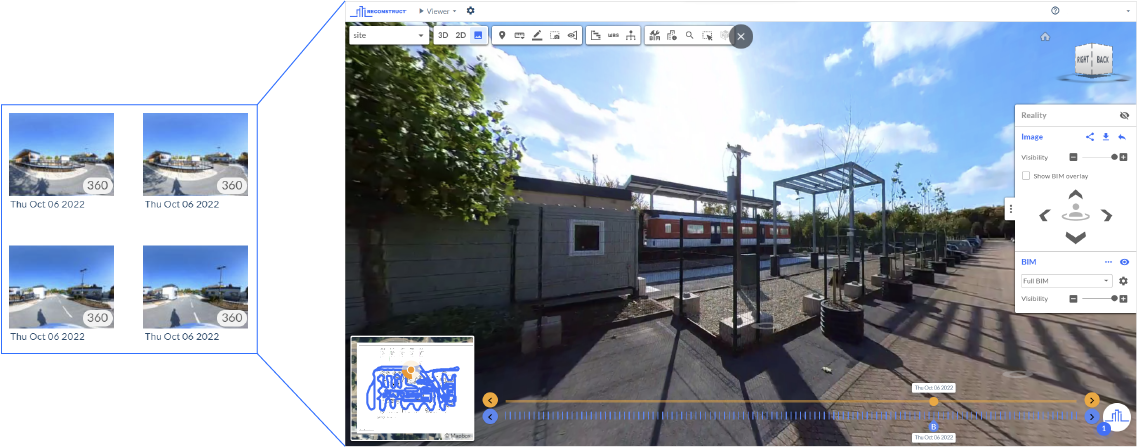
Construction Progress Monitoring: Best Practices for Remote Stakeholders
Remote construction progress monitoring provides stakeholders with faster, more streamlined visibility into construction progress—no travel required.
.png)
The Future of AI Project Monitoring in Construction
How long until a machine can monitor construction projects? New breakthroughs in three AI technologies may someday change how the industry works.