Reconstruct Helped OAC Services Save $30,000 on a Single Excavation Project
OAC Services (OAC) was building a large office campus in Silicon Valley for a top technology company.
"It only took a month to get our first 75 projects up and running with our new process. Reconstruct made it easy to get a capture bundle out to all project sites. We were able to spend less time in conversation about the projects and more time looking at the progress. We cut down time spent on the phone with GCs by 75%. The feeling of being on top of things came on strong."
The Problem
The process of quantifying the soil excavated and hauled away from the site was antiquated, inaccurate, time-consuming, and labor-intensive. The cost of exporting dirt from the site was roughly $90/ cubic yard. If not quantified and verified carefully, the cost could result in a bloated bill. When OAC received the bill for the soil removal, they knew they needed a way to confirm its accuracy.
The old-fashioned way of quantifying soil removal was through loading the dirt into trucks, using individual tickets per truck to determine the load, and trusting the vendor. The vendor was relying on rough estimates of volumes, which concerned OAC. OAC could hire a third-party survey crew to quantify and validate the amount of soil removal, but this option would be very costly with more overhead, time, and another contractor's bill.
OAC used Reconstruct to harness the data already being captured weekly through photogrammetry.
OAC used Reconstruct with drones and 360 cameras to monitor the progress of the project's exterior. In addition, Reconstruct performed automated volumetric measurements for earthwork with no additional effort. Then, OAC utilized the drone and 360 camera imagery to generate point clouds in Reconstruct to precisely measure cubic yards of soil removed and automatically track excavation progress over time. This included accurate quantification of the work completed and exact location coordinates.
When OAC received the bill for the soil removal, OAC compared the vendor's estimates with Reconstruct's data. The rough estimates were inaccurate, and the bill had been overpriced by $30,000.
The Results
Monica's team saved both time and money with their use of Reconstruct:
- 11 thousand hours saved on preparing progress reports.
- $7 million saved on avoiding rework.
- 80% increase in on-time project completion.
- $11 million saved on construction spent on schedule overages.
Related Content
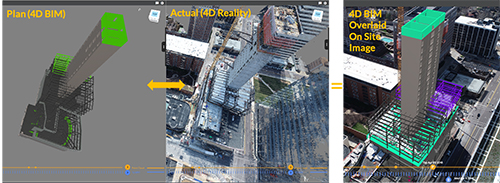
What is a Digital Twin for Construction?
Discover the benefits of digital twins and learn why this technology-fueled asset is revolutionizing how construction, engineering, and inspection stakeholders manage buildings.
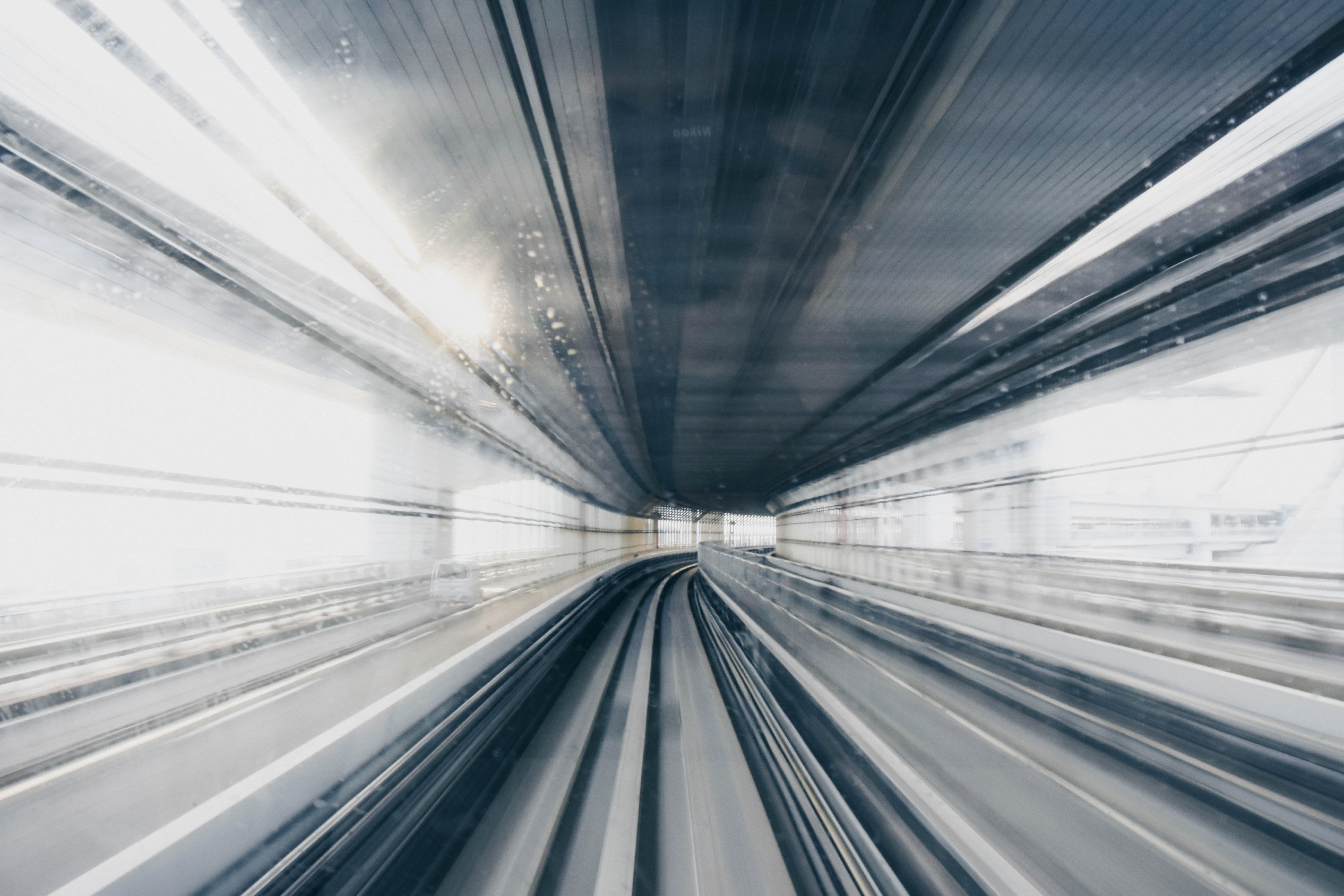
5 Innovative Ways Construction Professionals Mitigate Risk & Deliver On Time and On Budget
Discover 5 innovative strategies to mitigate construction risks and ensure on-time, on-budget delivery in this expert-led webinar.
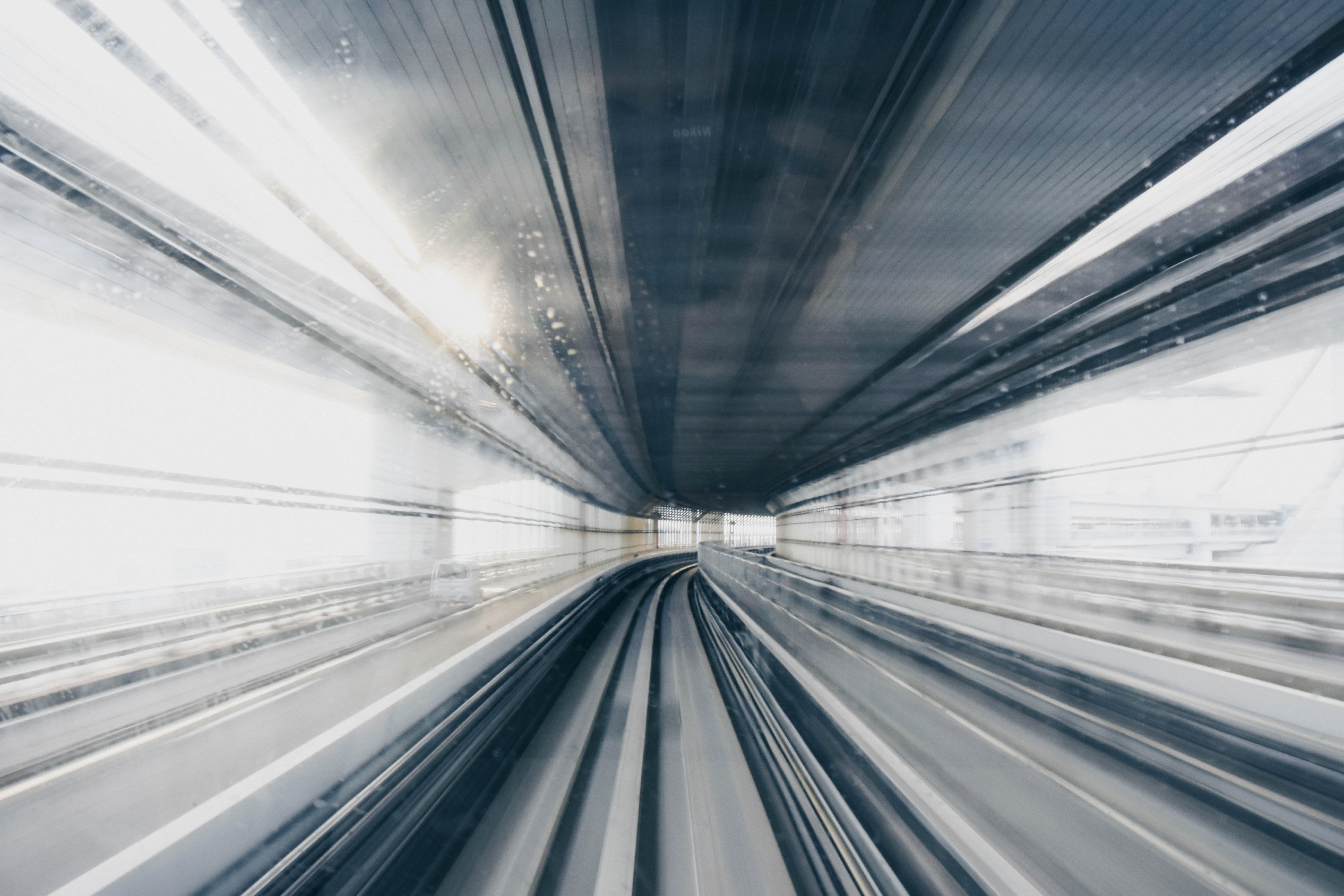
AI-Driven Digital Twins for 3D Reality Mapping and Virtual Inspection of Physical Assets
Learn AI-Driven Digital Twins for 3D Reality Mapping & Inspection! Join WJE & Reconstruct to enhance asset management decisions.