What is a Digital Twin for Construction?
What is a digital twin for construction?
Over the past decade, the construction industry has undergone a profound transformation, largely due to the integration of cutting-edge technologies that increase project efficiency, reduce travel costs, and improve project outcomes by optimizing communication between field teams and remote stakeholders. This is particularly true for the advent of the digital twin—a frequently updated virtual representation of a physical asset or an ongoing construction project that provides all stakeholders with a single source of measurable truth.
This article will define the concept of a digital twin for construction, review its benefits, and discuss why this technology-fueled asset is revolutionizing how construction, engineering, and inspection stakeholders manage buildings and structures throughout their entire lifecycles.
Key takeaways
- A digital twin is a virtual duplication of a construction project that is frequently updated with data on the actual performance of the project.
- These assets offer a 3D, immersive walkthrough of a job site over the timeline of the project, without the need for stakeholder travel
- This single source of truth—which can be measured, compared against plans and drawings, and combined with a schedule for 4D reality—improves stakeholder communication, optimizes decision-making, improves risk mitigation, and boosts productivity while ensuring safety and reducing miscommunications, costly rework, and delays.
What is a digital twin for construction?
In construction, a digital twin is a virtual representation of a physical asset, such as a building, structure, or infrastructure, that is frequently updated based on actual data from the project itself. A truly accurate twin is generated by a photogrammetry or reality mapping engine that automatically and precisely arranges images and video of a job site in space and over time, creating a measurable duplication of the project in 3D as immersive and precise as an in-person walkthrough.
The best reality mapping software to use for creating such digital twins should be hardware agnostic, allowing field teams to rapidly capture the reality job site using any device, not just highly-priced ones that require expert operators (i.e., LIDAR and Matterport scanners) but rather to complement them so the best of high-precision solutions (i.e., LIDAR) are brought together with high-quality visuals (Matterport scanners) and the ease and quickness of camera-based documentations. (Virtually any employee can capture the reality of a job site using hardware such as a smartphone or a 360 camera.)
Captured footage can be fed to a reality mapping engine regularly to create an online as-built that reflects the current reality of the project, providing stakeholders who may be 6,000 miles away with a real-time, dynamic model of the project that reveals every aspect of construction, since the very first day of work.
Related: Reality Capture vs. Reality Mapping: What’s the Difference?
Above, a 4D reality model generated with 360°, drone and smartphone images and videos taken over time.
Using 360 cameras and smartphones, Reconstruct generates measurable image-based digital twin walkthroughs and 3D point clouds for indoors and outdoors, over a project timeline.
Above, digital twins formed through the integration of 4D BIM and 4D reality models.
What are the benefits of using a digital twin for construction?
Four of the most common benefits of utilizing a digital twin in construction include improved alignment between remote and on-site teams, better decision-making, optimized risk mitigation, and enhanced productivity.
1. Enhanced collaboration between remote and seal teams
One of the most common construction pain points is misalignment between on-site teams and remote stakeholders. But when a digital twin is available to all groups, everyone from field teams to architects to engineers to contractors to owners can access and collaborate with a single source of truth. This enables better communication and coordination between all groups while reducing the need for pricey travel, time-consuming, on-site walk-throughs, and spending hours reviewing wordy reports that may not reveal the actual problems and issues offsite stakeholders need to see.
2. Optimized decision-making
Because a digital twin provides a real-time, immersive visualization of a job site, all stakeholders—not just the ones currently present—can inspect the status of a project. Moreover, the digital twin can be compared against schedule or even against 2D and 3D designs and drawings to perform error detection rapidly, pin concerns directly to visualized problems, and swiftly resolve any errors before they snowball into costly delays and rework.
Analyze progress, productivity, and risk for delays around each work location and collaboratively revise schedules in weekly contractor coordination meetings to tap off delay risks before they surface on your job site.
3. Improved risk mitigation
As mentioned above, a digital twin for construction offers remote stakeholders—including expert owners, owners’ representatives, inspectors, architects, engineers, and project schedulers—an in-depth look at a job site without the expense, stress, or constraints of frequent travel. As a result, construction risk management experts have more opportunities to identify potential risks and missteps throughout the construction process and even once a building is complete.
Regional project managers, project schedulers, as well as other executives can receive real-time, up-to-date data on the actual performance of their projects and have a data-driven approach to managing risk that’s visual and enables easy, quick communication regarding risk in the first place.
Online as-builts can also serve as a system of record for post-construction use cases, and these deliverables are often used for facility condition assessments and ongoing maintenance
Moreover, a digital twin can also protect stakeholders, including owners, after construction is complete. That’s because the digital twin creates a duplication of an asset along every step of a project’s schedule. As a result, stakeholders can simply rewind the clock on their digital twin to see where something was installed or how something was built should questions emerge or litigation arise.
Analyze and communicate construction progress deviations and risks for delays.
4. Boosted productivity and lowered cost of rework
A digital twin also allows for more streamlined, optimized construction processes, including more informative Owner/Architect/Contractor (OAC) meetings, more accurate scheduling, and faster visual quality assurance and quality control. Additionally, visual progress monitoring can be performed without restriction or travel, offering project managers true visibility into a job site instead of only what’s shown or reported to them from field teams’ reports.
Error detection, in particular, is especially efficient when performed using a digital twin. That’s because the best reality mapping tools allow stakeholders to pin concerns directly on problems and communicate the resolution of those issues swiftly—without constant, complicated communication across multiple channels. Action is taken as soon as an error is detected, the next steps are provided and assigned to a point person, and the issue is resolved immediately. All data—including the problem, how it was solved, and by whom—are recorded within the digital twin for future reference.
2D and 3D design integration, comparing projects against schedule, and using reality mapping to fill in the unavoidable gaps of 4D BIM also provide stakeholders with unprecedented insight into the status of a project. This data fuels productivity, ensuring all teams are focused on the project's safe, on-time, and at-budget completion.
Above, visual production models for interior work. Interior work space is mapped in 3D using 360° cameras, and a 4D BIM, color-coded based on trade contractor responsibilities, is overlaid to compare reality vs. plan for progress and quality deviations.
About Reconstruct
Reconstruct is a pioneer of reality mapping technology and has set the gold standard for digital twins in the construction, inspection, and engineering industries. From airports to hospitals to retail stores to college campuses, project stakeholders from every vertical have integrated efficient, intuitive reality mapping into their construction processes. These organizations have been able to slash travel time and expenses, improve visibility into their projects, optimize communication between all teams, and walk away from finished jobs with online as-builts that serve as the basis for facility condition assessments, potential renovation and refurbishment planning, and protection against liability for years to come.
To learn more about Reconstruct or schedule a demo of how a digital twin can help your organization reap these benefits, contact our team.
Related Posts
The History of 3D Reality Mapping with 360 Cameras
Reconstruct released the reality mapping technology needed to 3D model job sites from 360 cameras in 20156, transforming remote project monitoring.
.png)
How to generate 3D point clouds from both 360 and drone reality capture
Blend indoor 360 video capture and outdoor drone capture for one integrated 3D reality mapping system.
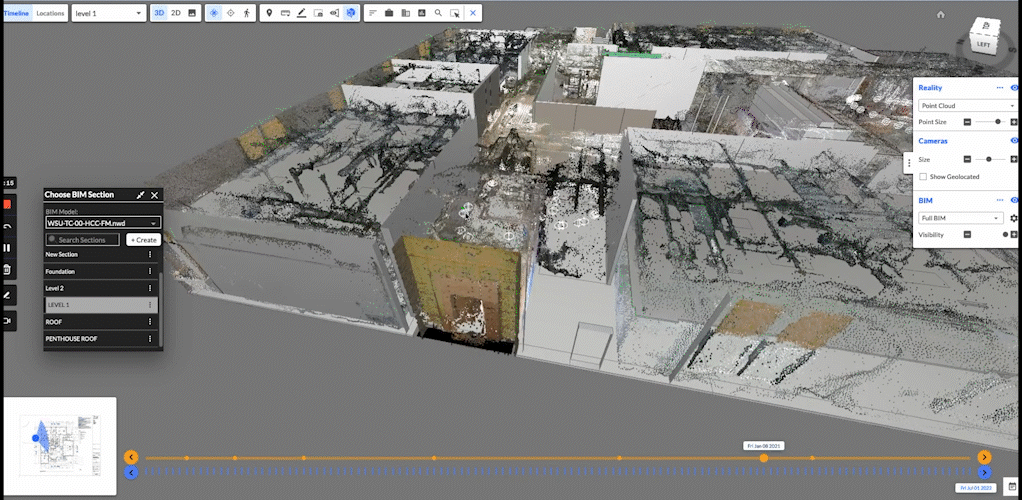
Four Reasons to Consider a Digital Twin for Construction
Four reasons why more stakeholders are relying on digital twins for construction, including frequent progress monitoring and optimized quality control.