3 Benefits of Measurable As-Builts in Retail & Multi-Site Construction
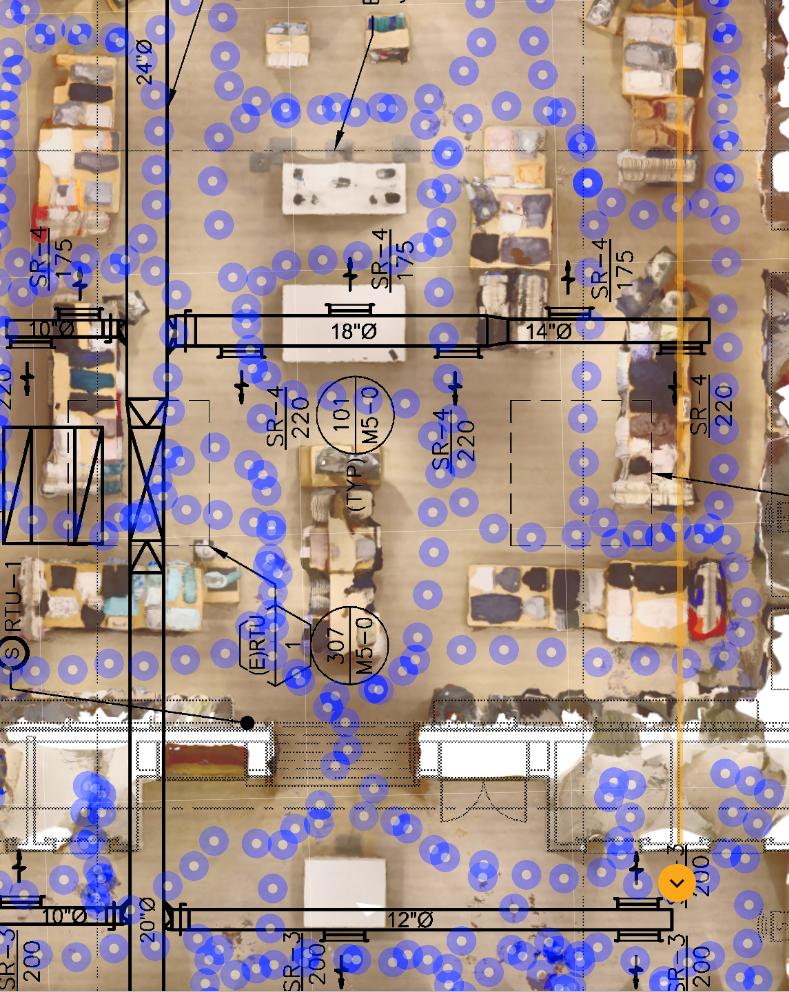
Many workflows in the Architecture, Engineering, and Construction (AEC) industry, such as construction monitoring, condition assessments of existing facilities, or scan-to-designs for renovation projects, can benefit from an online, 3D as-built representation of a structure or asset. In this article, we’ll zero in on how measurable, accurate as-builts generated by reality mapping engines benefit stakeholders in the retail and multi-site construction stakeholders.
Key takeaways:
- 2D and 3D as-builts offer accurate documentation of any project site, such as an existing convenience store that doesn’t have any ground truth that represents its current conditions or a project under construction.
- Unlike as-designed floor plans, these as-builts are generated automatically by reality mapping engines and provide a ground truth of as-is conditions, right when you need them.
- Advances in reality mapping technology allow virtually any on-site employee to rapidly capture store imagery using devices like a smartphone or 360 camera. Captures of a small store take about 10 minutes.
- Once automatically transformed into 2D floor plans and 3D models, this documentation can be used for physical asset inspection, site survey, condition assessment, quality control and quality assurance, future renovations and planning, and more.
- Online as-builts allow remote stakeholders to virtually walk, measure, and inspect job sites or use them for operations and maintenance tasks without dispatching a team of engineers to conduct a survey. Instead, a photogrammetry engine can quickly create the basis for an engineering-grade floor plan while engineers remain at their desks.
As-builts enable facility condition assessment for thousands of widespread stores.
For many companies in the retail space, portfolios of stores are not in the dozens… but in the thousands. When assets are spread across the country, performing frequent and in-depth facility condition assessments can become costly, time-consuming, and even downright impossible. Fortunately, advances in photogrammetry allow offsite stakeholders to visualize stores and job sites thousands of miles away.
In fact, the best reality mapping engines can transform raw video footage of a job site or finished store into a precise, completely measurable, and truly immersive floor plan and 3D model. A gas-stationed-size store takes only 10 to 15 minutes to scan, and footage is automatically pinned in space and over time, creating accurate documentation of current conditions almost instantly.
Insights generated from these assessments enable remote corporate stakeholders, including regional engineers and portfolio managers, to perform punch list walkthroughs and sign off on stores that adhere to brand consistency guidelines. Stakeholders can also remotely zero in on problems and concerns that require a closer look. So long as the reality mapping technology utilized offers intelligent communication and collaboration tools, the assessor can pin concerns and action items directly onto visualized issues, with accurate documentation of location and time for the issues of interest.
Whenever necessary, the right team can be physically dispatched to the job site for further inspection or to make repairs. However, by implementing virtual facility assessment using online as-builts first, these companies significantly expedite the resolution of outstanding issues and also benefit from reducing the time and money spent on unnecessary travel to job sites.
360 capture of construction site
Reconstruct creates a measurable 3d model and corresponding 2d floor plan of your construction site
Related: Physical Asset Inspection vs. Visual (Remote) Asset Inspection
Stakeholders can remotely measure, inspect, and compare design versus reality.
Another key benefit of as-built documentation for retail and multi-site stakeholders? The ability to inspect, measure, and overlay design drawings and plans against a store's captured reality.
Reconstruct, for example, allows stakeholders to measure every inch of a store without ever stepping inside. Any on-site employee can perform rapid reality capture using a device as simple as a smartphone or 360 camera. After a 3D, immersive digital model and a corresponding 2D floor plan are generated, these assets can be shared as a single source of truth amongst all teams, including local management, inspectors and engineers, regional managers, and corporate stakeholders.
Moreover, stakeholders can also overlay 2D and 3D design drawings and plants atop as-built documentation. This allows even offsite teams to compare what's there versus what should be there, understand future plans for renovation, and more.
Reconstruct recently worked with a department store to inspect and punch list 400 store-in-stores in 36 states over an ambitious four-month timeframe. The company’s in-house construction team was small and centralized, and contractors and fixtures teams were limited.
Using reality mapping, site surveying occurred at 25 sites a week over the weekends. On Mondays, the company’s corporate team and fixture contractors worked together (from different locations) to review the surveys. To instantly identify installation errors, teams overlaid design drawings atop as-builts. Any detected issues were immediately resolved. Reconstruct’s pinning and issue-tracking capabilities were also used to create, verify, communicate about, and resolve punch lists before handoff.
By using online, measurable as-builts instead of in-person walkthroughs, the company required no additional staff to manage the project, slashed travel to sites for inspection, and drastically reduced contractor rework, delays, and site revisits.
At the end of the project, the department store also walked away with 400 online as-builts of its store-in-stores to use for future planning; renovation; and maintenance, repairs, and operations.
Reconstruct transforms all images into a measurable 3D point cloud
Related: Remote Quality Control: The Secret To Avoiding Costly Rework
Stakeholders automatically receive a measurable 2D floor plan to inform all future decisions.
Another reason reality mapping benefits those in the retail and multi-site construction space? The technology automatically generates accurate, 2D, as-is representations that can be used to generate engineering floor plans. Typically, when a company requires a current floor plan of a store, an executive dispatches an engineer with a surveying crew to the store. Once an appointment is secured, this team travels to the site and uses tape or laser measurement tools and a piece of paper to manually create a floor plan.
But with reality mapping, companies can rapidly obtain accurate as-is documentation of their stores, which allows them to have their engineers remotely create engineering-grade floor plans.
Even a store manager can perform reality capture in minutes, providing off-site stakeholders timely access to a floor plan (and more) that answers the same questions. These 2D floor plans are highly accurate and linked to the imagery that provides additional information about where things are located, how the store is laid out, and whether specific updates or installations are contextually feasible.
This context is essential. After all, a floor plan alone will never answer the same questions as an immersive walkthrough. But with photogrammetry, even corporate stakeholders who’ve never visited the job site can quickly identify the repercussions of increasing the size of a walk-in freezer or narrowing the width of a drive-through lane. And all this work—including instant measuring—can be performed from a desk thousands of miles away.
Online as-builts are powerful forms of documentation that allow stakeholders to answer questions about a store at once. There's no need to wait for an expert to find time on their schedule to survey a site, ask a manager for a picture of this or that, or request an employee measure a certain area when they get a break in their day. Instead, up-to-date documentation about a store's current condition is available to all stakeholders anytime, anywhere. They can measure any corner of the store on the spot.
About Reconstruct
Reconstruct is the leader in digital twins for construction, empowering on-site and remote stakeholders with highly accurate and measurable 2D floorplans and 3D models of job sites and stores. To learn more about how reality mapping technology can streamline your company’s facility condition assessments, feel free to contact our team or request a personalized demo.
Related Posts
.png)
Key Benefits of As-built Documentation in Construction
As-built documentation offers stakeholders accurate measurements of completed work, expediting pay applications, renovations, and more.
.png)
The Future of AI Project Monitoring in Construction
How long until a machine can monitor construction projects? New breakthroughs in three AI technologies may someday change how the industry works.
Reconstruct Customers Share 2023’s Top Construction Challenges
From laser scanning inefficiencies to reality capture path confusion, here’s how Reconstruct’s reality mapping software solved top construction challenges.