Photogrammetry for Construction 101
In the built environment, photogrammetry is the technology used to turn 2D images or videos of an active construction site or an existing physical asset into a 3D representation (also known as a digital twin.) In this article, we’ll further define photogrammetry, explain how the technology works, and review the most common ways photogrammetry is utilized in the construction industry.
Key takeaways:
- Photogrammetry transforms images and videos into accurate, “as-built” models of a structure or scene. This process, also known as reality mapping, provides stakeholders with precise, measurable 2D and 3D duplications of a site.
- Photogrammetry is a technology that connects the dots between images and video footage, then accurately “reconstructs” whatever is visualized in 3D, often in 3D point clouds and 3D mesh models. It can also create 2D orthophotos and floor plans.
- In construction, photogrammetry empowers better site analysis and surveying, as-built documentation, clash detection and coordination, remote project monitoring and planning (with or without 4D scheduling), and condition assessment of existing structures and infrastructure.
What is photogrammetry?
Photogrammetry is a technology that transforms aerial and ground-level images and videos into surveys and maps of both built and natural environments. In other words, photogrammetry extracts accurate 3D information from dimensional footage, generating “as-built” models (or digital twin replicas) of an object, scene, or structure.
How does photogrammetry work?
Photogrammetry uses triangulation to generate accurate, 3D duplications of real-world scenes and structures.
Using hardware as simple as a smartphone or 360 camera, a person (or drone, or robot) “captures” the reality of the site. Next, by feeding the photogrammetry engine multiple photographs of a scene from different angles, the overlapping areas in the images are used to determine the position and shape of the objects in three-dimensional space. This is accomplished by identifying common features in the images, including corners or other points of interest, and matching them between different photos.
Once the photogrammetry engine has intelligently connected all footage in space and over time, the result is a “reconstructed” reality map of the structure or scene in 2D or 3D. These “reality maps” can be point clouds, mesh models, orthophotos, and floor plans.
Related: Is NeRF Technology the Future of Reality Mapping?
How is photogrammetry used in construction?
Photogrammetry is used in construction in various ways, including site analysis and surveying, as-built documentation, clash detection and coordination, remote project monitoring with or without 4D scheduling, and facility condition assessment.
Site analysis and surveying
Photogrammetry is often used to rapidly survey construction sites, even before construction begins. Whether capturing topographic data using a drone or asking an employee to perform a “reality capture walk” of a gas station before it’s refurbished into a coffee shop, photogrammetry can provide stakeholders with accurate surveys of both indoor and outdoor conditions.
These site surveys can help with design, plans, scheduling, permitting, and more.
Visualized above: The unique ability of Reconstruct’s photogrammetry engine to create color floor maps from 360 videos, smartphone videos, as well as drones or time-lapse cameras mounted on tower cranes (crane cameras).
Online as-builts
An online as-built is the final documentation of a completed construction project. Online as-builts allow remote and on-site stakeholders to refer to a structure’s “digital twin” from anywhere, anytime, at any point along the construction timeline.
With an online as-built, stakeholders can turn back the clock to see through walls, optimize repairs and maintenance, record conditions during handover, prepare for renovations, or resolve claims during litigation.
Visualized above: Photogrammetry produced a 3D point cloud using a 360 video, mapped against a 2D design.
Clash detection and coordination
Clash detection refers to comparing design-vs.-design or design-vs.-reality to ensure no two parts of a project building (e.g., plumbing, structural beams, etc.) interfere with one another. During construction, photogrammetry enables a true comparison of reality against design, allowing even remote stakeholders to simply explore whether the design fits existing conditions and if the field team is constructing the most recently coordinated and issued-for-construction design models.
Visualized above: Measurable images produced through photogrammetry against design for clash detection and visual quality assurance and quality control during construction.
Constructability reviews via 4D digital twins
When BIM is combined with reality data and construction schedule, stakeholders can visualize the next construction steps atop a duplication of the actual job site.
4D digital twins that simultaneously represent both reality and design over project timeline can also identify potential conflicts caused by simultaneously-occurring construction activities weeks before those tasks begin. By visualizing planned work sequences in lookahead meetings, stakeholders can review implementation of coordinated BIM, preemptively identify scheduling conflicts, then adjust construction schedules, saving rework, time, and money while improving safety.
4D digital twins also allow for remote progress tracking and the ability to measure real work-in-place quantities, assess the quality of that work-in-place, and lean on information from the job site to update the project schedule and speed up payment applications. 4D scheduling also improves project understanding, ensuring team members are clear on the next construction steps so they can perform even the most complex installations correctly the first time.
Related: What is 4D BIM (4D Scheduling)?
Remote project monitoring
With photogrammetry, construction stakeholders can perform precise, frequent project monitoring without stepping foot on the job site. And because the most cutting-edge photogrammetry engines can use even the simplest forms of reality data, it’s easier than ever before to provide remote stakeholders with an updated, accurate digital twin of a construction site.
Citygate, the Nordic region’s tallest office building, uses Reconstruct photogrammetry software and Insta360 cameras to enable remote project monitoring. Accurate, measurable 2D floor plans and 3D models allow offsite stakeholders to compare progress against schedule, measure what’s been built against what’s been planned, and inspect every inch of the job site for quality and safety.
Visualized above: Photogrammetry is a time machine for construction, producing reality models over project timelines for visual progress monitoring.
Visualized above: A 4D digital twin displaying integrated 4D reality vs. 4D BIM for construction progress monitoring
Infrastructure inspections and facilities assessments
Finally, photogrammetry allows stakeholders to assess the current state of a building or infrastructure via physical asset inspection. These “as-builts” can streamline maintenance, repairs, and operations, all while slashing the time required on a job site and disruption to tenants.
If reality capture was performed during construction, stakeholders can rewind these digital twins to see through walls to inspect now-hidden installations, quickly providing insight without the cost, delay, or disruption of demolition.
Visualized above: Photogrammetry-produced point clouds and 2D orthophotos are used to inspect bridges, chimneys, and tunnels, among other types of physical assets.
How accurate is photogrammetry in surveying?
The accuracy of photogrammetry depends on several factors, including the quality of the footage and imaging hardware, the amount of footage provided, the quality of the photogrammetry engine used, and the skill of the hardware operator. When properly performed, photogrammetry can be extremely accurate, often down to the centimeter—or even millimeter.
Precisely how accurate of a measurement a stakeholder requires should be a determinant in selecting what tools, technologies, and teams are needed to capture reality. Reconstruct recently co-conducted an experiment at the Oracle Industries Lab that identified how to choose the right tool for reality capture, given resources, budget, and use case.
About Reconstruct
Reconstruct—a reality mapping pioneer—offers a next-generation, cloud-based photogrammetry engine that can transform virtually any form of reality data into 2D and 3D reality maps. Almost anyone can conduct reality capture, no expertise required, using hardware as simple as a smartphone or 360 camera. Footage from drones, laser scanners, and more is also readily accepted by Reconstruct, and all footage can be mixed and matched.
Unlike other providers, only Reconstruct’s photogrammetry engine can create 3D models from 360 videos. It is also the only engine that can process both standard and 360 images and videos.
Related Posts
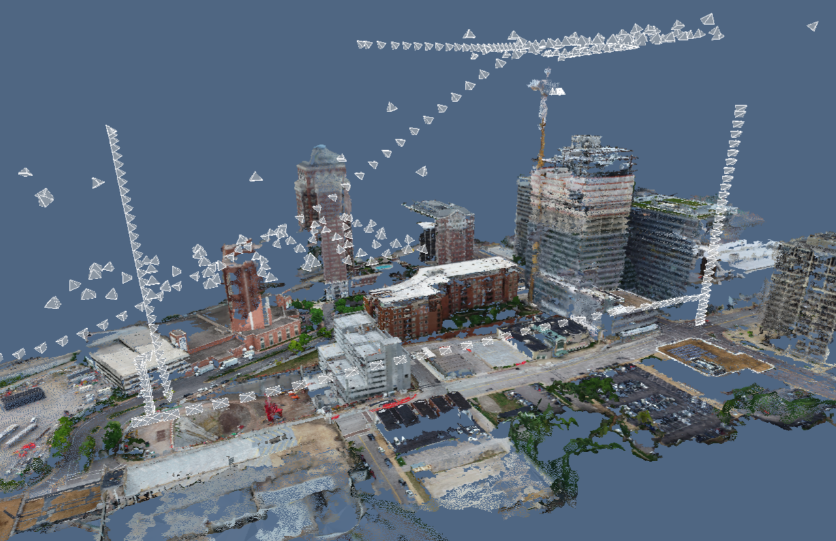
What is photogrammetry software for construction?
Photogrammetry software, in construction, extracts geometric information from 2D reality capture images to create a 3D “digital twin” of the job site.
.png)
Reconstruct adds Structured .e57 Point Cloud Import
Reconstruct adds Structured .e57 Point Cloud Import to the Visual Command Center: All Forms of Reality Capture Can be Viewed with a Consistent Image-based...
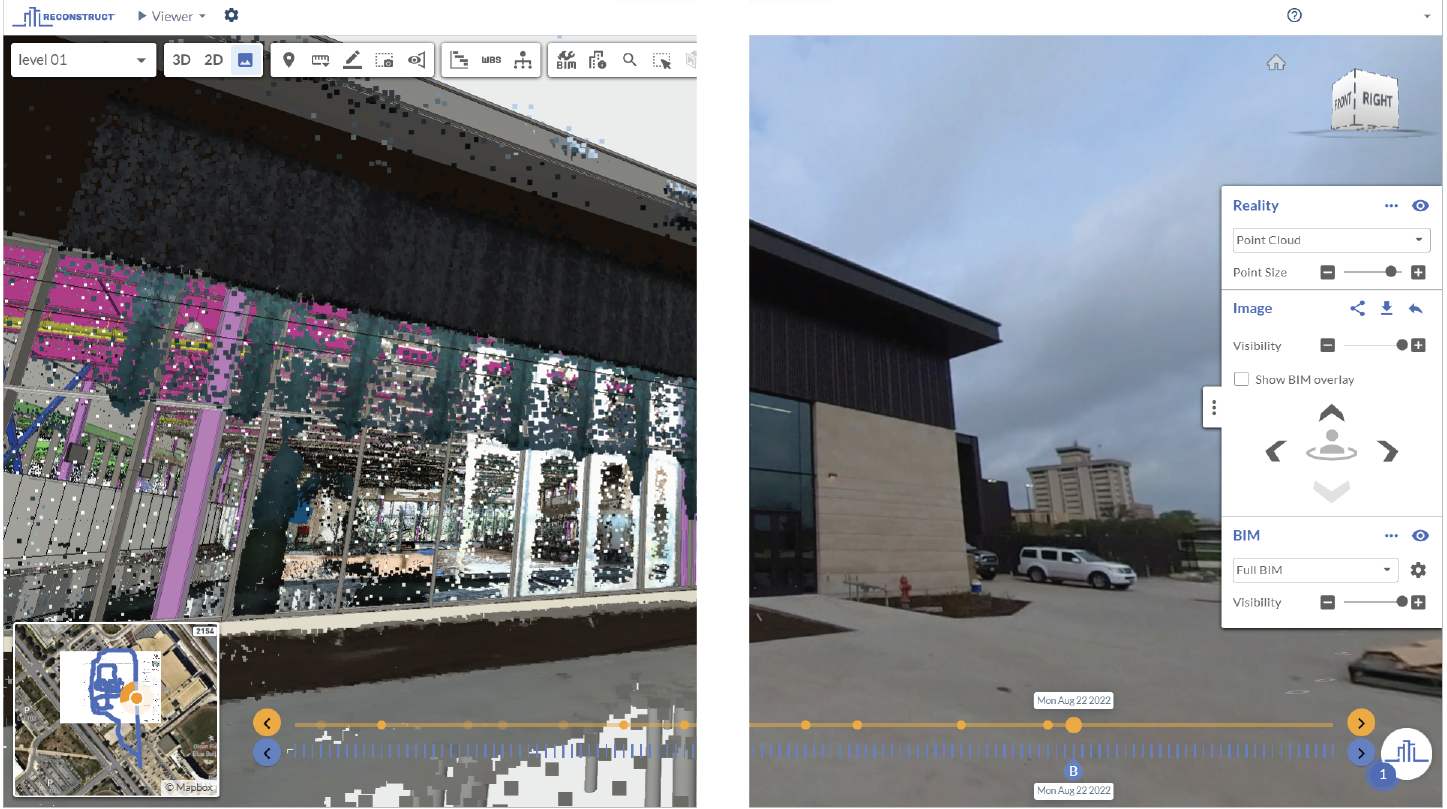
Why engineers are using reality mapping to “capture” site inspections
Site inspections, which are mandated by law, can be digitally archived via reality mapping technology for improved visibility and legal protection.