Construction Quality Control | 4 Benefits of Remote QA/QC
Quality assurance (QA) and quality control (QC) are central to ensuring a construction project's ongoing and final success. QA and QC must be performed frequently as part of a construction progress monitoring strategy. Fortunately, cutting-edge technology has enabled quality assurance and quality control efforts to be performed remotely, reducing costs while retaining all of QA/QC’s benefits.
In this article, we’ll zero in on some key benefits of frequent, virtual quality assurance and quality control.
Key Takeaways
- Virtual quality assurance and quality control occur when stakeholders utilize digital site surveys of a job site to set field teams up for success pre-installation and then validate work after installation.
- Many organizations use reality mapping technology to supplement on-site QA/QC, vastly increasing the number of experts able to perform QA/QC without the high costs associated with job site travel.
- Chief benefits of QA and QC include preventing delays, preventing overrun costs, and reducing the cost of rework.
- By performing reality capture to enable remote progress monitoring and QA/QC, organizations also unlock as-built documentation that can protect them against liability claims or be used to prepare for tenant improvements.
To practice quality assurance and quality control, stakeholders must have their eyes on the job site regularly. This requires either regular travel to the job site or the implementation of reality mapping technology that brings the job site directly to the stakeholders. When reality mapping software is used, stakeholders enjoy the following:
1. Improved construction quality
By implementing virtual, remote QA and QC at every stage of construction, site inspectors can identify and address potential issues early on, significantly improving the overall quality of the construction project. Quality assurance is preventative—it refers to the proactive measures taken so that a problem or issue never arises. On the other hand, quality control refers to the inspection and approval of already completed work.
For example, during quality assurance, a QA stakeholder (such as a contractor or engineer) ensures a wall is placed in the exact right space. They may draw lines on the floor to match wall placement in design drawings and plans. During quality control, once the wall is built, a QC stakeholder will verify the measurements and placement of the wall.
Using 2D and 3D design integration tools, many of these processes can be performed remotely with the utmost accuracy. With Reconstruct, for example, stakeholders can overlay design drawings and plans atop the “digital twin” of the job site to visualize plans over reality or compare what’s there against what should be there.
2. Reduced cost of rework
One of the chief benefits of practicing quality assurance and quality control is that both strategies can reduce overall project costs. Rework is expensive, time-consuming, and often unnecessary, and optimizing QA and QC efforts can slash costs. Of course, quality assurance is best for this. After all, getting something right the first time is always the goal.
But as long as quality control is performed frequently, QC can also significantly reduce rework costs by identifying and addressing little problems before they snowball into costly, major concerns. The earlier an issue is caught and corrected, the lower the costs and likelihood of project disruption or delay.
Reality mapping software and construction monitoring software can help lessen the costs of rework by empowering remote stakeholders to carefully inspect construction frequently…without the need for (or cost or stress of) travel.
Related: 10 Benefits of Visual Progress Monitoring for Construction Stakeholders
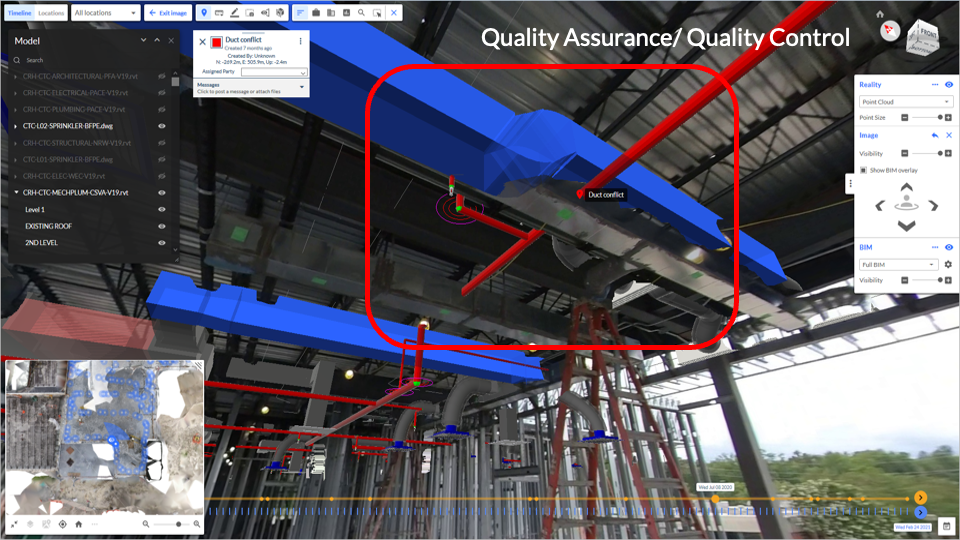
Reconstruct’s measurable pictures allow project team members to check the quality of their installations against coordinated MEP models.
3. Improved compliance and legal protection
Another key reason for performing regular quality assurance and quality control is to ensure compliance with standards and regulations. Such compliance ensures that a structure is safe and that all stakeholders do everything possible to avoid noncompliance's legal and financial consequences.
Moreover, for those who perform remote or virtual QA and QC, as-built documentation that captures construction progress over time can also protect against legal claims in the future.
Plus, because photogrammetry software such as Reconstruct allows users to turn back time and review construction as captured at any given date or time, stakeholders can inspect the job site (and what’s hidden beneath sealed walls) without the cost of disruption of demolition.
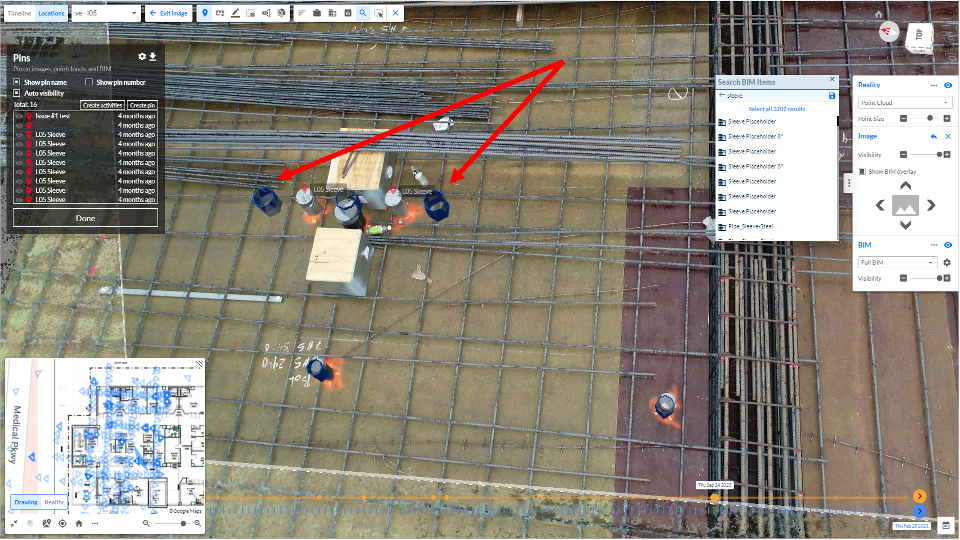
Misplacement of boxouts, sleeves, conduits, and embeddings are some of the most common construction quality issues during the placement of concrete. Reconstruct allows project teams to measure as-built installations and compare them against project specifications and when available against 2D and 3D design.
4. Reduced QA/QC costs
Because in-person quality assurance and quality control are time-consuming and expensive, many organizations have two choices: dedicate ample resources to keep inspectors and experts on-site or perform frequent reality capture so that remote stakeholders can immerse themselves in the job site without travel.
By creating a virtual duplication of the job site, organizations can expand the circle of people who perform quality assurance and quality control. Having a documented, as-built digital twin of the construction project means that anybody anywhere can simply log in and check in on their specific part of the project at a fraction of the cost and in a sliver of the time. (For users who don’t have a login, Project Snapshot allows Reconstruct users to curate a quick, pre-planned and shareable tour of a job site accessible in a single click.)
Instead of paying to bring ten experts to the job site, organizations can have one person performing inspections on the job site while sending out the digital twin to the other experts so they can verify design, installation, and more remotely.
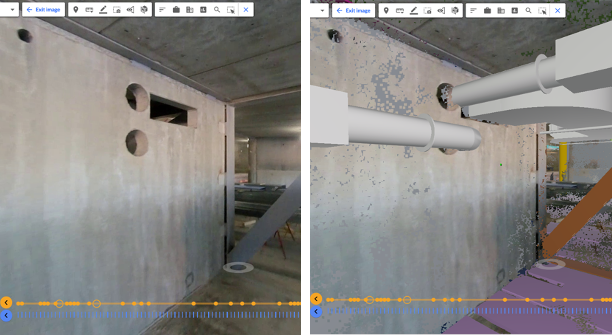
During the commissioning phase of the project, Reconstruct design overlays allow yet another quality control step. The ability to overlay BIM on images and point clouds generated from reality helps Reconstruct users identify quality issues early on. It also allows VDC team members to update their as-designed 2D and 3D drawings into as-builts by documenting and updating the design based on how actual installations look.
5. Fast turnaround on detailed, focused QA/QC tasks
Reconstruct users can benefit from the addition of smartphone video to the capture app, which allows them to use smartphone videos to quickly capture and create 3D models and measurable walkthroughs of specific areas of the project. This new feature enables anyone on site to capture reality without the need for a 360 camera or training. While smartphone cameras have a limited field of view (since they are not 360 cameras), they compensate for that by having high resolution and great low-light performance. This makes smartphone capture a great solution for in-wall utilities, pre-concrete placement, underground utilities, and under-ceiling MEP inspections.
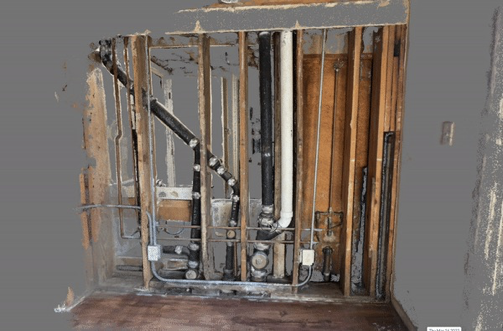
Above, an in-wall inspection as captured by a smartphone for construction quality control. Such captures can be performed on readily available equipment, quickly, and with low light and recording conditions.
About Reconstruct
Reconstruct is the leader in digital twin technology, empowering stakeholders all over the world to perform frequent, remote quality assurance and quality control. Using reality mapping technology, any job site can be duplicated virtually, making regular QA/QC possible for organizations of every size and projects of every budget.
To see your project in Reconstruct, schedule a demo today.